Сегодня завершилась 24-ая международная специализированная выставка «МЕТАЛЛООБРАБОТКА-2024» «Оборудование, приборы и инструменты для металлообрабатывающей промышленности».
Для нас это мероприятие прошло плодотворно, интересно и полезно!
В рамках выставки наши специалисты провели большое количество важных и интересных встреч с почетными гостями. Так, на нашем стенде побывали:
- заместитель министра промышленности и торговли Иванов Михаил Игоревич;
- руководители департаментов министерства промышленности и торговли РФ;
- руководитель Федерального агентства по техническому регулированию и метрологии — Антон Павлович Шалаев;
- помощник главы республики Татарстан Альберт Харисович Гильмутдинов;
- мэр города Зарафшан, Республика Узбекистан Назирбек Рахманов;
- а также блогер Евгений Супер.
В рамках выставки «Металлообработка-2024» был подписан меморандум об установлении дружественного сотрудничества и обмена опытом в сфере лазерных и аддитивных технологий между ГК PLASAR и Республикой Узбекистан. Со стороны группы компаний подписантом выступил Дмитрий Олегович Чухланцев, со стороны Узбекистана — мэр города Зарафшан — Назирбек Рахманов.
Надеемся, что и для всех гостей выставка была полезна!
До встречи на следующих выставках! 🤝
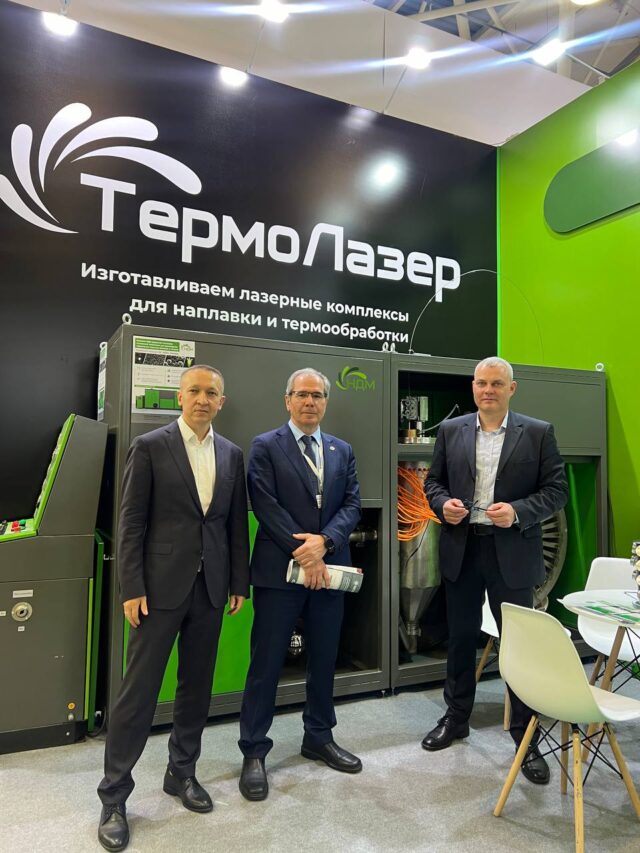
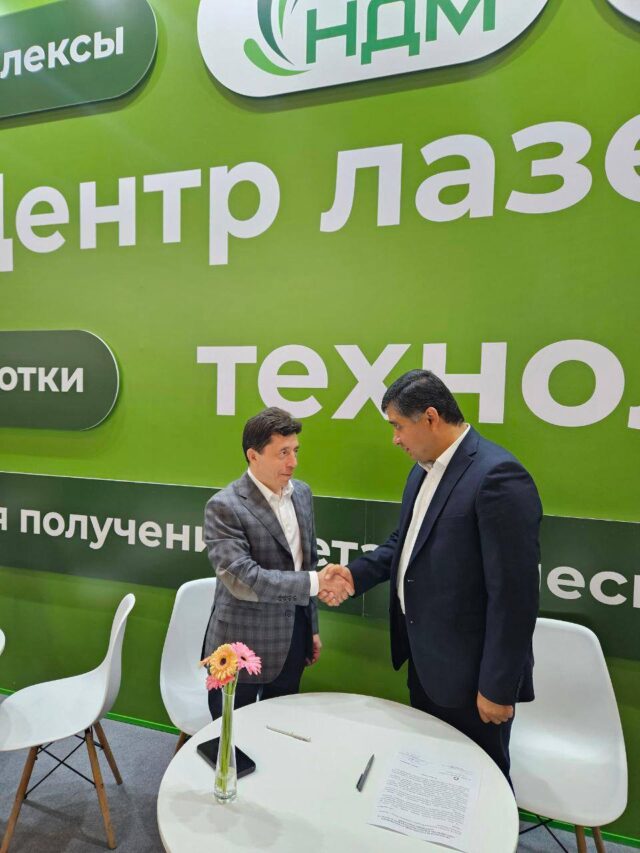
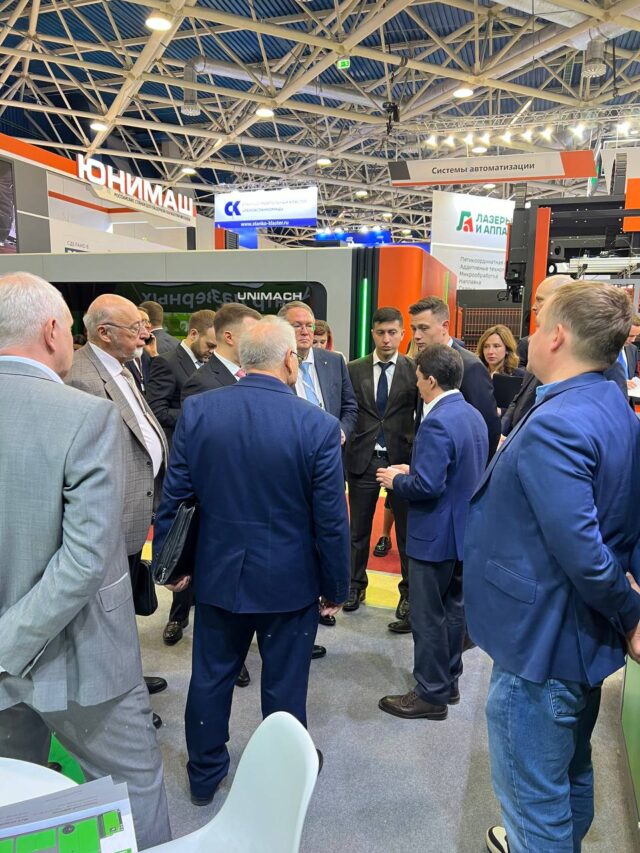

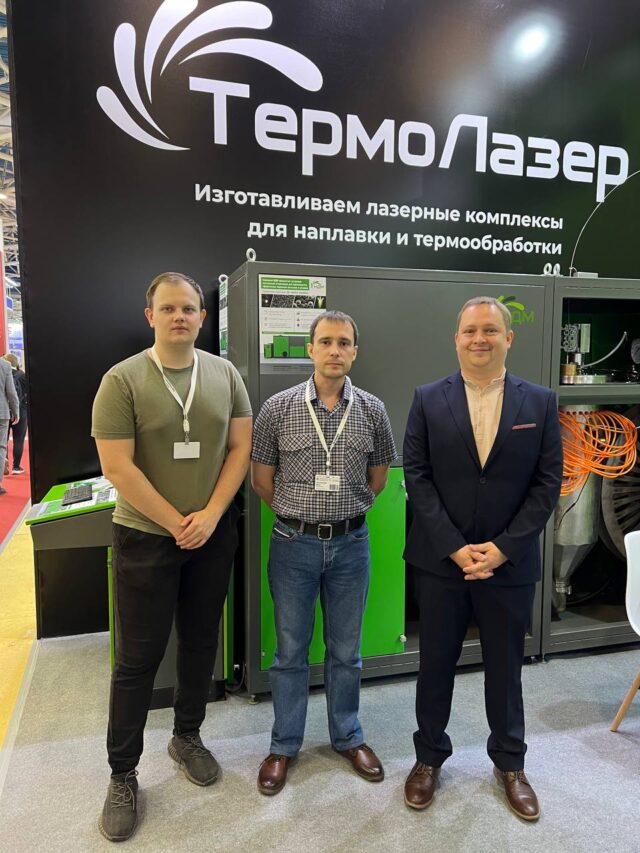
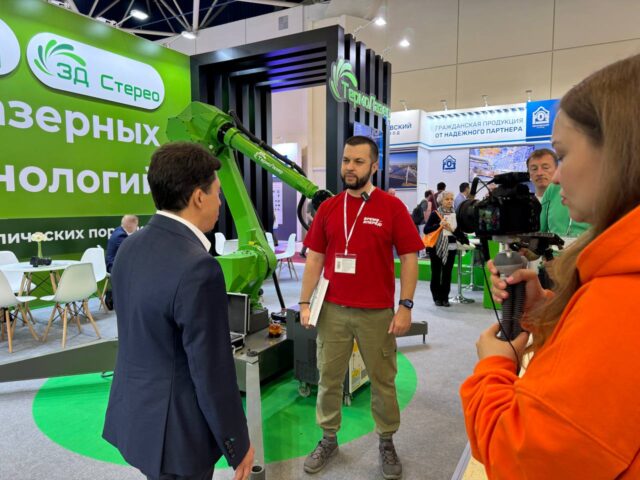